
How to identify the quality of High Pressure Resin Hose
Release time:
2021-09-15
There are two types of rubber hoses: High Pressure Resin Hose and Low Pressure Rubber Hose. High Pressure Resin Hose is generally composed of an outer rubber layer, a steel wire reinforcement layer, a middle rubber layer and an inner rubber layer. The inner rubber layer is in direct contact with the hydraulic oil and is generally made of synthetic rubber.
There are two types of rubber hoses: High Pressure Resin Hose and Low Pressure Rubber Hose. High Pressure Resin Hose is generally composed of an outer rubber layer, a steel wire reinforcement layer, a middle rubber layer and an inner rubber layer. The inner rubber layer is in direct contact with the hydraulic oil and is generally made of synthetic rubber. The load-bearing capacity of the hose is determined by the reinforcement layer, which is the skeleton of the hose and is usually braided or wound with steel wire. Most of High Pressure Resin Hose use steel wire braid as skeleton, and most of them use steel wire winding skeleton. The outer rubber layer is generally made of rubber with good wear resistance and corrosion resistance to ensure that the reinforcement layer is not damaged by mechanical damage, chemical corrosion, moisture and rust. The low-pressure hose is made of braided cotton and twine instead of braided steel wire, which is generally used for low-pressure oil return. pipeline.
The inner and outer layers of the High Pressure Resin Hose pipe wall are made of oil-resistant rubber, and the middle is (2 to 4 layers) of cross-braided steel wire or wound steel wire. Poor quality hose will appear: the thickness of the hose wall is uneven; the wire braid is too tight, too loose or the number of steel wire layers is too small; the deformation of the hose (elongation, shortening or bending deformation) after pressurization is large; the outer layer of rubber Poor air tightness leads to corrosion of the steel wire; poor sealing of the inner layer of glue allows oil to easily enter the steel wire layer; insufficient adhesion between the glue layer and the steel wire layer. The above conditions will reduce the bearing capacity of the hose, and eventually burst at the weak point of the pipe wall. During assembly, if the crimping amount is too small, that is, when the pressure between the joint and the hose is too loose, the hose may come out of the joint at the beginning of use under the action of oil pressure; If it is too tight, it is easy to cause the inner layer of the hose to be partially protected, resulting in cracks, and the oil will directly enter the steel wire layer from the rupture, and then escape along the gap between the steel wires to the end of the jacket, or it will continue to run along the steel wire layer to accumulate somewhere. Make the outer layer of rubber bulge and even crack. When the High Pressure Resin Hose and the joint are assembled, if the crimping speed is too fast, it is easy to cause damage to the inner rubber and rupture of the steel wire layer, which will cause the hose to be damaged prematurely in use.
When replacing the hose by High Pressure Resin Hose, the length of the hose, the number of steel wire layers, the shape and size of the joint should be reasonable, and the bending degree of the hose should be minimized; when tightening the joint nut, the hose should not be twisted or too large. The bending and twisting of the hose will greatly reduce the service life of the hose; protective measures should be taken for some parts that are prone to friction to prevent the hose from bursting due to wear.
Related news
undefined
Mobile Website
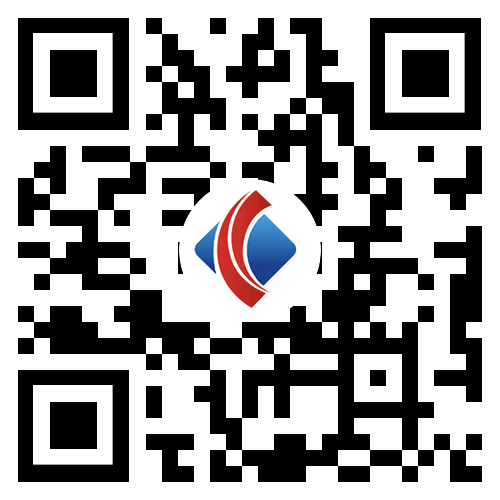
Hebei Keweite Pipeline Equipment Co., Ltd.
Tel: +8618332535575
Mail:zfmn1234@gmail.com
Address: Meidel Industrial Park, Chengxi Development Zone, Jingxian County, Hengshui City, Hebei Province
Copyright © 2022 Hebei Keweit Pipeline Equipment Co., Ltd.